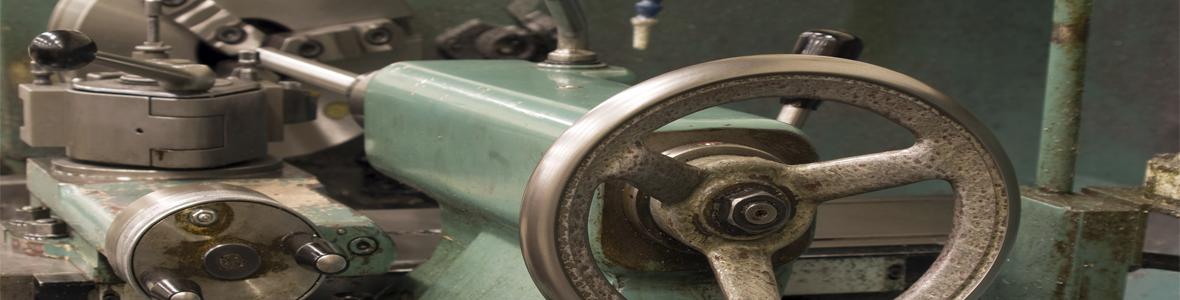
Job Shop
Lead-time Reduction
Problem
Customer orders were rising and this shop could not keep up with demand. As a result, lead times became more than what they were quoting their customers. They were at risk of losing customers. As lead times increased so did the stress levels within the business.
Solution
- Reduced load on the Inspection process by sample inspecting
- Introduced automated inspection for speed and accuracy
- Improved process for Material Control
- Implemented kanbans for consistent flow
Results
- Cut lead time by 20%
- Increased overall capacity by 5%
- Obtained annual hard savings of $450,000
Medical Device Manufacturer
Eliminating waste and reducing variation
Problem
When transitioning from Research and Development to Production, there was much waste and variation. During the transition it became evident that the defect rates and productivity were not acceptable.
Solution
- Applied 5S to improve flow
- Performed an MSA (measurement system analysis) to improve measurement system
- Through DOE (design of experiments) redesigned weld process for optimum settings
- Introduced new method of cutting
Results
- Rolled First Pass Yield went from 20% to 67%
- Production rates went from 43 minutes per unit to 15 minutes per unit
- Defect rates went from 30% to 10%
- Obtained annual hard cost savings of $238,000
Some of the other manufacturing related projects we have supported
Reduced:
- Lead times for job shop
- Set-up times on assembly line
- Defects and scrap on window film manufacturing
- Cost of poor quality related to quality systems
- Scrap cost of packing materials
- Defects on laminate composites
- Packing material costs and environmental impact
- Variation of foam application
- Emulsion defects
- Plastic injection molded scrap
- Delamination of acrylic sheet
- Defect rate of tissue sectioning
- Returned goods
- Waste and variation to meet FDA requirements
- Inventory, distance and pick times for medical device manufacturer
- Change over times for food processing
Improved:
- Forecast accuracy
- Quality of tube welds
- Inventory accuracy and cut overtime
- Revenue and profit from new line layout
Faster and more efficient:
- Quality assurance for product development
- Design of lead frames
- Order fulfillment (pick/pack/ship)
- RMA (returned material authorization) process
Increased:
- Capacity of test and calibration
- Production output for cell manufacturing
- Productivity of switch assembly
- Medical device quality yield
- Overall capacity through more efficient inspections
- Preventive maintenance effectiveness (more uptime)
- Profit through tool redesign and facility layout
- Inventory turns of plastics manufacturer
- Capacity with new facility installation