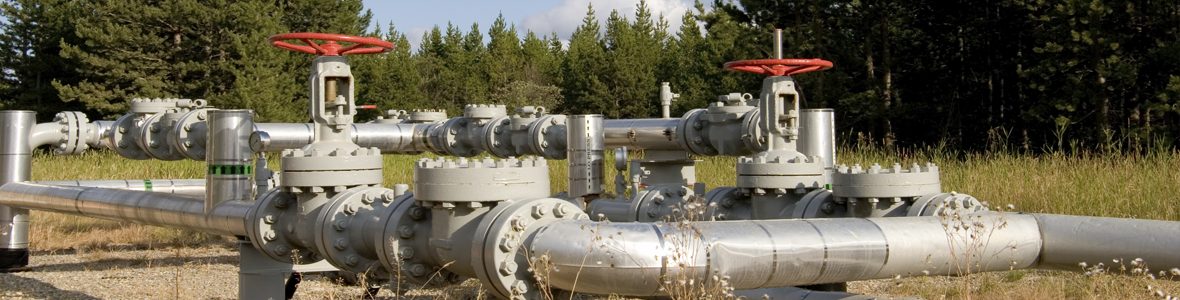
Oil Stimulation
Cost savings from increased efficiencies
Problem
A ramp up in production demand resulted in poor practices that were showing on the bottom line. Lost product due to long stimulation processes were hurting the contracted stimulator as they were hit with late penalties and the well owners were hurt by lost production.
Solution
- Re-sequenced specialties for dual path work
- Applied mistake proofing to the control valves
- Co-located and line balanced and created cross functional teams
- Applied 5S and visual controls
Results
- On-site distance traveled was 287 miles and is now 38 miles
- Downhole monitoring productivity increased by 34%
- Increased overall production by $50,000,000 per year
Bulk Transportation and Storage
Improved delivery and cost savings
Problem
The delivery process was costly and on-time delivery was poor. There was a lack of accountability and the measurement systems were inaccurate.
Solution
- Modified processes and equipment to hold the right amount at the right place
- Created a new position responsible for overall bulk flow
- Changed method of clean outs between deliveries
- Improved accuracy of the measurement system to reduce write-off losses
Results
- Reduced write-off losses by 65%
- Overall annualized cost savings of $14,000,000
Some of the other projects we have supported:
Reduced:
- Cost of tank cleaning and maintenance
- Mistakes and unsafe conditions for service shop
- Late delivery and stress through heijunka scheduling
- Field service set-up times
- Job site morning start-up times
- Inventory carrying costs for oil field supplies
- Installation costs for drains at construction sites
Improved:
- Off shore steel plate installation productivity
- Bulk plant visual appearance and flow through
- Test equipment storage and control
- Parts availability and inventory accuracy for pipe and valves
- Safety and productivity of tank maintenance
- Pipe support installation response time
- Equipment maintenance response time
Faster and more efficient:
- Pump maintenance and repair
- Storage and retrieval of consumable supply items
- Permit renewal process
- Test lab for field samples
- Truck refurbish process
- Well stimulation process
Increased:
- DOT (Dept of Transportation) speed and accuracy of tracking
- Lab regulation compliance
- On-time arrivals to job sites
- Capacity of valve test and calibration
- Flow sensor build and repair productivity
- Well head maintenance uptime and quality
- Maintenance rig efficiency and capacity